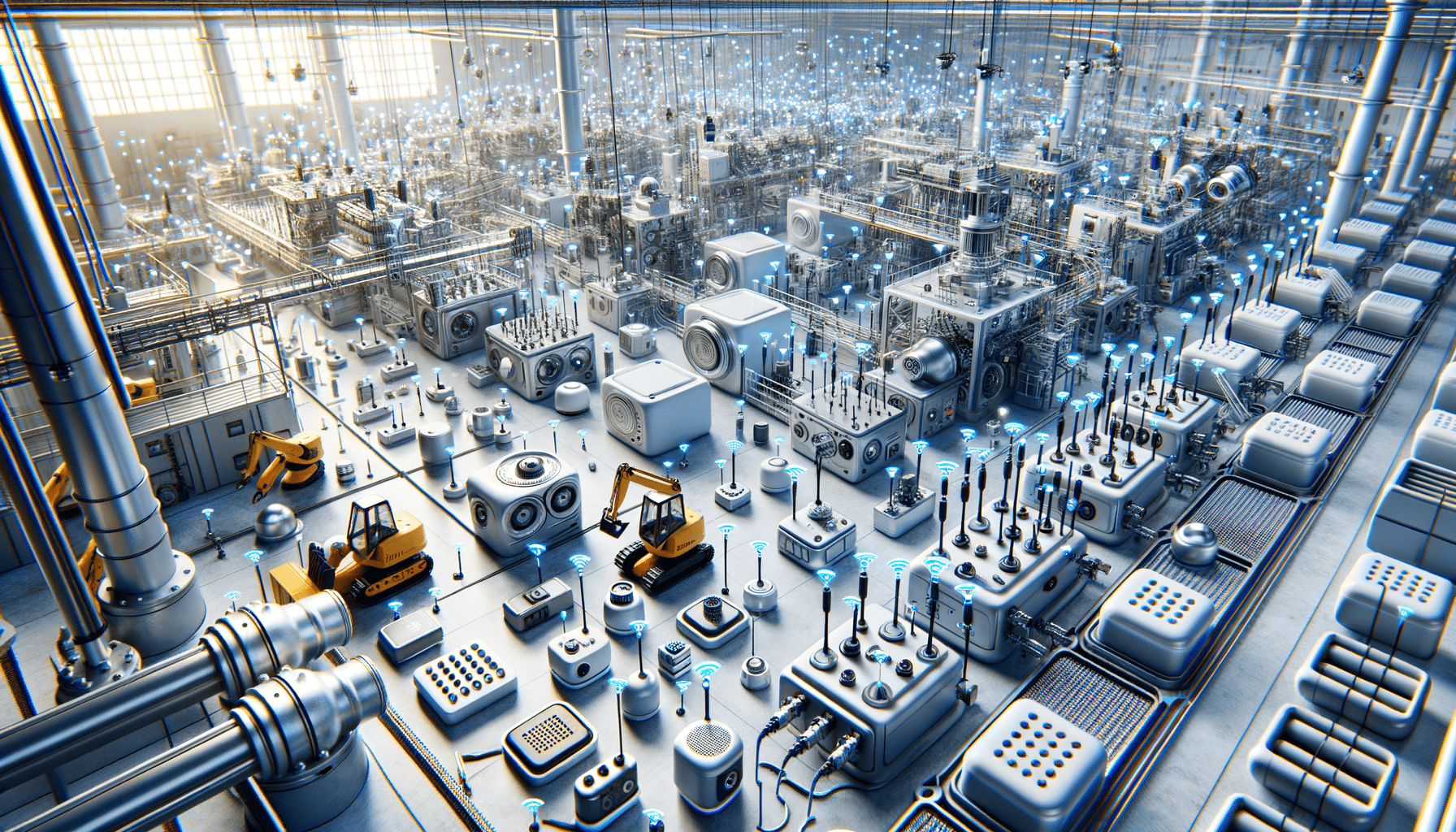
Exploring the World of Wireless Industrial Sensors
Introduction to Wireless Industrial Sensors
In the modern industrial landscape, efficiency and precision are paramount. Wireless industrial sensors are at the forefront of this technological evolution, providing industries with the tools they need to monitor operations seamlessly. These sensors play a critical role in various sectors, from manufacturing to logistics, by offering real-time data collection and analysis. With the rise of the Internet of Things (IoT), the integration of wireless sensors has become more prevalent, allowing industries to operate more intelligently and efficiently.
The significance of wireless industrial sensors lies in their ability to provide continuous monitoring without the constraints of physical wiring. This not only reduces installation costs but also enhances flexibility in sensor placement. As industries strive for greater automation and data-driven decision-making, these sensors are becoming indispensable tools in achieving operational excellence.
How Wireless Industrial Sensors Work
Wireless industrial sensors function by transmitting data from the physical environment to a central system where it can be analyzed and used for decision-making. These sensors come equipped with various technologies, such as radio frequency (RF), Bluetooth, and Wi-Fi, to facilitate wireless communication. The choice of technology often depends on the specific requirements of the application, such as range, data rate, and power consumption.
One of the key advantages of wireless sensors is their ability to be deployed in hard-to-reach or hazardous environments where traditional wired sensors would be impractical. This capability opens up new possibilities for monitoring conditions in remote locations, such as oil rigs or mining sites. Furthermore, wireless sensors can be integrated with cloud-based systems, enabling remote monitoring and control, which is particularly beneficial for industries with multiple locations.
Wireless sensors typically consist of three main components: the sensing element, the processing unit, and the communication module. The sensing element detects changes in the environment, such as temperature, pressure, or humidity. The processing unit converts this data into a digital format, and the communication module transmits it to a central hub for analysis.
Applications of Wireless Industrial Sensors
Wireless industrial sensors have a wide array of applications across different industries, each leveraging the technology to enhance their operations. In manufacturing, these sensors are used for predictive maintenance by monitoring the health of machinery and equipment. By analyzing data on vibration, temperature, and other parameters, manufacturers can predict when a machine is likely to fail and perform maintenance proactively, reducing downtime and costs.
In logistics and supply chain management, wireless sensors are employed to track the location and condition of goods in transit. This real-time tracking capability ensures that products are stored and transported under optimal conditions, reducing spoilage and improving customer satisfaction. Additionally, wireless sensors are used in environmental monitoring to track air and water quality, contributing to compliance with regulatory standards and promoting sustainability.
Another significant application is in the energy sector, where wireless sensors monitor infrastructure such as pipelines and power grids. These sensors provide critical data on pressure, flow rates, and other variables, enabling operators to detect and address issues before they escalate, ensuring the safety and reliability of energy supplies.
Challenges and Considerations
Despite their numerous advantages, the deployment of wireless industrial sensors comes with its own set of challenges. One of the primary concerns is ensuring reliable communication in environments with potential interference from other wireless devices or physical obstructions. To mitigate this, industries must carefully plan the placement of sensors and choose the appropriate communication technology.
Power management is another critical consideration, as wireless sensors typically rely on batteries. Ensuring a long battery life requires balancing power consumption with the frequency of data transmission. Some sensors are equipped with energy-harvesting capabilities, such as solar power, to extend their operational life.
Security is also a significant concern, as wireless sensors can be vulnerable to cyberattacks. Industries must implement robust security protocols to protect data integrity and prevent unauthorized access. This includes encryption of data transmissions and secure authentication mechanisms.
The Future of Wireless Industrial Sensors
As technology continues to advance, the future of wireless industrial sensors looks promising. The integration of artificial intelligence (AI) and machine learning with sensor data is expected to drive further innovation, enabling more sophisticated analysis and predictive capabilities. This will allow industries to not only react to current conditions but also anticipate future trends and challenges.
Moreover, the development of 5G technology is set to enhance the capabilities of wireless sensors significantly. With faster data transmission speeds and lower latency, 5G will enable more complex and data-intensive applications, further expanding the potential uses of wireless sensors in industrial settings.
In conclusion, wireless industrial sensors are poised to play a pivotal role in the digital transformation of industries. By providing real-time insights and enabling smarter decision-making, they will continue to drive efficiency and innovation across various sectors.